Introduction
Quality management is a fundamental aspect of any organization that aims for long-term success. It ensures that products and services meet customer expectations, regulatory requirements, and industry standards. Effective quality management not only improves efficiency but also enhances customer satisfaction, reduces costs, and fosters a culture of continuous improvement.
This article explores the fundamental principles and practices of quality management, explaining how organizations can implement them effectively. Whether you are a business owner, quality manager, or an employee looking to understand the importance of quality management, this guide will provide valuable insights.
What is Quality Management?
Quality management refers to the process of overseeing all activities and tasks that must be completed to maintain a desired level of excellence. It includes the determination of a quality policy, creating and implementing quality planning and assurance, and quality control and improvement measures.
Key Components of Quality Management
- Quality Planning – Identifying the quality standards relevant to the project or organization and deciding how to meet them.
- Quality Assurance (QA) – Ensuring that quality requirements are fulfilled through systematic processes.
- Quality Control (QC) – Monitoring outcomes to verify that they meet established standards.
- Continuous Improvement – Implementing strategies to enhance quality over time.
Principles of Quality Management
The principles of quality management are based on internationally recognized frameworks such as ISO 9001. These principles help organizations achieve excellence and customer satisfaction.
1. Customer Focus
The primary goal of quality management is to meet and exceed customer expectations. Understanding customer needs and delivering products or services that satisfy them is crucial for long-term success. Businesses that prioritize customer satisfaction gain loyalty and positive word-of-mouth, which leads to growth.
2. Leadership
Strong leadership is essential for maintaining a quality-driven culture. Leaders must set clear goals, align quality objectives with business strategies, and inspire employees to take ownership of quality improvements.
3. Engagement of People
Quality management is a collective effort. Engaging employees by providing training, encouraging feedback, and fostering teamwork helps create a culture where quality is everyone’s responsibility.
4. Process Approach
Organizations achieve efficiency by structuring activities into clear, defined processes. The process approach ensures that all tasks contribute to the overall quality goals, reducing variability and waste.
5. Continuous Improvement
Continuous improvement (Kaizen) is a core aspect of quality management. Businesses should constantly assess their processes, identify inefficiencies, and implement improvements to enhance performance.
6. Evidence-Based Decision Making
Data-driven decision-making ensures that quality improvements are based on factual analysis rather than assumptions. Organizations should use key performance indicators (KPIs) and feedback mechanisms to monitor quality trends.
7. Relationship Management
Maintaining strong relationships with suppliers, stakeholders, and customers is vital for ensuring consistent quality. Collaborative relationships foster trust, efficiency, and shared success.
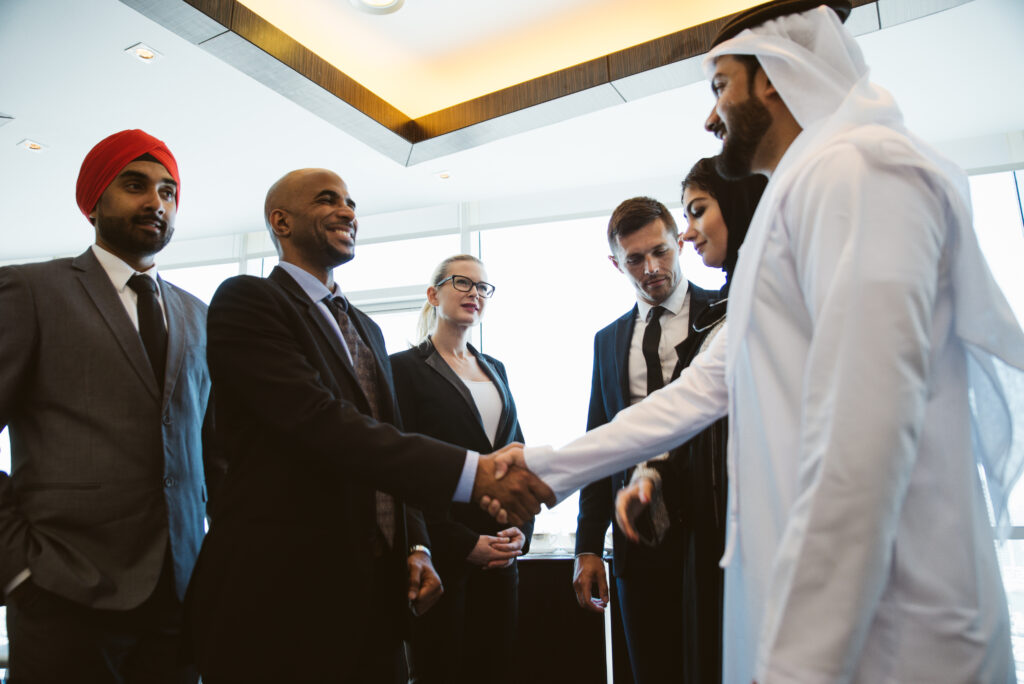
Total Quality Management (TQM)
What is TQM?
Total Quality Management (TQM) is a holistic approach to long-term success that focuses on customer satisfaction. It integrates all organizational functions, including production, marketing, finance, and customer service, to ensure quality is embedded in every aspect of the business.
Key Principles of TQM
- Customer-Oriented Approach – Every decision and process should be aimed at enhancing customer satisfaction.
- Employee Involvement – Engaging employees at all levels ensures collective responsibility for quality.
- Process-Centered Approach – Standardizing and improving processes leads to consistent quality output.
- Integrated System – Every department and function should align with quality objectives.
- Strategic and Systematic Approach – A well-defined quality strategy ensures long-term success.
- Continuous Improvement – Constantly refining processes leads to greater efficiency and product quality.
- Fact-Based Decision Making – Using data and analysis helps organizations make informed quality decisions.
- Mutually Beneficial Supplier Relationships – Strong supplier partnerships contribute to better quality control.
Benefits of TQM
- Improved customer satisfaction and loyalty
- Reduced operational costs and waste
- Enhanced employee morale and engagement
- Better compliance with industry standards and regulations
- Increased competitive advantage in the market
Implementing TQM
Organizations can implement TQM by:
- Providing employee training and education
- Establishing clear quality objectives
- Encouraging open communication and feedback
- Conducting regular quality assessments and audits
- Using tools like Six Sigma and Lean methodologies
Practices of Quality Management
Organizations implement various quality management practices to ensure they meet industry standards and customer expectations. Below are some widely used methods:
1. Six Sigma
Six Sigma is a data-driven methodology that aims to eliminate defects and reduce process variations. It uses statistical tools and techniques to improve efficiency and consistency in operations.
2. Lean Management
Lean principles focus on eliminating waste and improving productivity. By streamlining processes and removing non-value-adding activities, organizations can enhance efficiency and reduce costs.
3. ISO 9001 Certification
ISO 9001 is an internationally recognized quality management standard that helps businesses implement a structured approach to quality. Organizations that achieve ISO 9001 certification demonstrate their commitment to maintaining high-quality standards.
4. Quality Control Tools
Several tools are used to ensure quality control, including:
- Check Sheets – Used for collecting and analyzing data.
- Pareto Charts – Helps prioritize issues based on their impact.
- Cause-and-Effect Diagrams (Fishbone Diagrams) – Identifies the root cause of quality problems.
- Histograms – Shows data distribution for better decision-making.
Benefits of Quality Management
Implementing a strong quality management system provides several benefits, including:
- Increased Efficiency – Streamlined processes reduce errors and enhance productivity.
- Cost Reduction – Minimizing defects and waste reduces operational expenses.
- Enhanced Customer Satisfaction – Consistently meeting customer expectations builds trust and loyalty.
- Regulatory Compliance – Quality management ensures that businesses adhere to industry and legal standards.
- Improved Employee Engagement – A quality-driven culture motivates employees and enhances teamwork.
- Competitive Advantage – High-quality products and services set businesses apart from competitors.
Challenges in Quality Management
While quality management offers many benefits, organizations may face several challenges in implementation:
- Resistance to Change – Employees may resist adopting new quality processes.
- High Implementation Costs – Initial investments in training and certification can be expensive.
- Lack of Leadership Support – Without strong leadership, quality initiatives may fail.
- Inconsistent Processes – Poorly defined processes lead to variability and inefficiency.
.
Conclusion
Quality management is essential for organizations seeking long-term success. By understanding and implementing key principles and practices, businesses can improve efficiency, enhance customer satisfaction, and gain a competitive edge. The adoption of frameworks like ISO 9001, Six Sigma, Lean Management, and TQM can drive continuous improvement and ensure compliance with industry standards.